The Walmart Supplier Quality Excellence Program (SQEP)
Learn about defects, how you can avoid them, and how you can dispute them
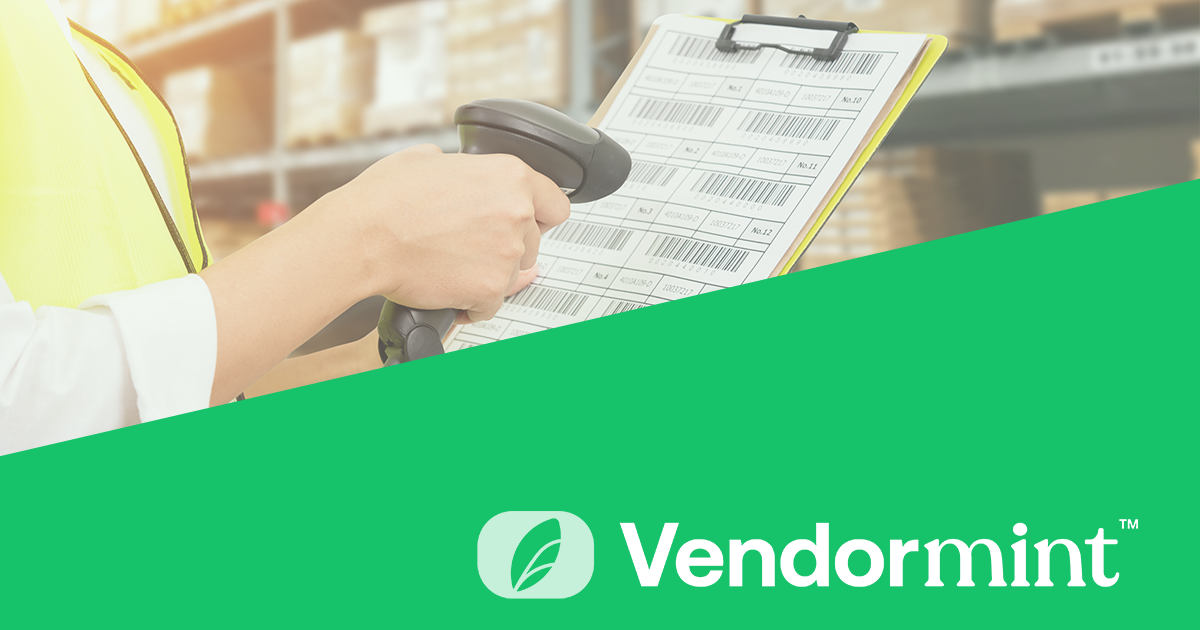
On February 1, 2021, Walmart rolled out a program to ensure a “defect-free” supply chain. This program is called the Supplier Quality Excellence Program (SQEP). Unlike On Time In Full (OTIF) metrics, SQEP affects all Walmart suppliers, including e-commerce and omnichannel.
It’s important to note that SQEP standards are constantly evolving, as it is a new compliance program. Ensure you are checking Retail Link and Supplier One for news on SQEP. Walmart has manuals and guides for SQEP that it regularly updates, sometimes as often as twice a year.
SQEP focuses on the “four rights:”
- Right item
- Right condition
- Right invoice
- Right time
The program came out in phases and focuses on different supply chain standards, including:
- Document accuracy
- Barcodes and labeling
- Packaging, pallet, and load quality
Let’s dive into these.
Document Accuracy
All Walmart suppliers must have an electronic data interchange (EDI) connection with Walmart using the AS2 standard. The connection must be consistent and provide accurate documentation per SQEP.
Walmart defines document accuracy on two levels: purchase order (PO or EDI 850) accuracy and Advance Ship Notice (ASN or EDI 856) accuracy. The general idea is that the contents of the shipment and its associated documents align and connect before the shipment arrives at the distribution center (DC).
SQEP defects for PO accuracy and ASN accuracy are as follows:
- Overage: The number of cartons or cases is greater than what was on the original PO. Read more about overages, shortages, and damages.
- Canceled PO: You ship an order against a canceled PO.
- Canceled Line: You ship a product on a PO after the line item was canceled.
- Item Not on PO: You ship an extra item or replace an item with a different UPC than what was listed on the PO.
- Wrong Pack: The quantity shipped on the vendor pack (i.e., cases) level doesn’t match the PO.
- Recall/Withdrawal: There is a recall on an item, or you have withdrawn the item from Walmart’s shelves.
- Date Issue: An item violates the date agreement. For example, this can occur if you ship a food item after its Best-By date.
- Not Walmart Freight: You ship items that are not Walmart items.
- No ASN Label (only affects Direct Store Delivery Consolidation—DSDC): Your cases are missing the 18-digit Serial Shipping Container Code (SSCC) label.
- ASN Not Downloaded (only affects DSDC and Pharmacy—D38 suppliers): Walmart was unable to download your ASN.
- No ASN Received: Walmart says you didn’t send any ASNs for the order.
- ASN Error: Your ASNs fail Walmart’s business validations. This can mean that your ASN is missing vital data or not formatted correctly.
- Late ASN: Your system sent the ASN after your order arrived at the receiving DC.
- Rework: The DC had to alter the item’s packaging into one of these configurations:
- Relabel
- Poly bag
- Box
- Tape
- Any other rework at the DC
- Allocation Issue: There was an issue with sorting your order, or it was assigned to the wrong store.
- Imagery (e-commerce only): There are missing or incomplete item images on Walmart.com.
- Item Setup: The item information is missing, incomplete, or inaccurate in Item 360.
- Parent-Child: The “child UPC” is not linked or incorrectly linked to the “parent UPC.” This occurs when you have a hierarchy of items and format the Universal Product Codes (UPCs) incorrectly.
Walmart fines suppliers for document inaccuracies based on the defect. The ASN Not Downloaded defect is unique and only applies to DSDC and Pharmacy (D38) suppliers.
The ASN Not Downloaded defect calculation for DSDC and Pharmacy is:
$200 flat fee per defective purchase order
The ASN Not Downloaded defect calculation for all other departments is:
$25 flat fee per defective purchase order
Walmart’s fine structure for all other document inaccuracies is:
$200 per defect + $1 per case
So, if you have a PO with the 12 cases, and you have 1 rework defect and 1 inaccurate ASN, your fine would be:
$412 = [$200 x (1 + 1)] + ($1 x 12)
Barcodes and Labeling
Phase 2 of SQEP involved barcodes and package labeling. Three defect areas fall under this category:
- Barcode compliance
- Label compliance
- Hazardous materials (Hazmat) compliance
Each defect area has sub-defects and requirements based on merchandise alignment. Additionally, Walmart fines defects based on either inspection (using a person) or automation (using technology).
The barcode, labeling, and hazmat non-compliance calculation for defects found by inspection is:
$200 administrative fee per defect per PO + $1 per package with defects
The calculation for defects found by automation is:
$1 per case with defects
So, for a shipment of 9 packages manually inspected with 1 barcode defect on 3 cases and 1 labeling defect on 6 cases, the fine would be:
$409 = [$200 x (1 + 1)] + [$1 x (3 + 6)]
Barcode Compliance
Walmart defines barcode compliance defects by formatting, quantity, legibility, and other issues. The following are barcode sub-defects:
- Wrong Format: The shipment contents have barcodes, but they are not in the correct format. For example, the barcode has the GTIN-12 instead of the GTIN-14 UPC.
- Barcode Not on Two Sides (Incorrect Quantity): There is a barcode, but only on one side of the package. Walmart requires a scannable barcode on at least two sides of the carton or case, and these must match each other and the contents.
- No Barcode Found (Missing Barcode): The carton or case does not have any barcodes on any side.
- VNPK GTIN Does Not Match Item Setup (Incorrect Barcode): The vendor pack GTIN-14 barcode is in the approved format, but it does not match the contents of the package according to Item 360 or Item Setup.
Walmart uses radio frequency identification (RFID) scanners to identify the contents of packages received at its DCs, so proper barcoding is essential.
Labeling Compliance
Labeling compliance involves ensuring that your shipment labels are clear, accurate, and informative. The defect will appear as “General Case Marking Compliance” on the SQEP scorecard.
This defect is separated into sub-defects, some of which only affect e-commerce suppliers, while others have separate label requirements depending on the merchandise alignment or shipping network (DSDC or direct import). For example, shoes and apparel require a Walmart item number, and DSDC shipments must have scannable barcodes on the inner packs within the case as well.
These sub-defects are:
- Carton Marking Not on Two Sides (Incorrect Quantity): There are labels and markings, but they are only on one side of the box.
- Item Description Not Found (Missing Item Description): Your labels or markings do not contain a proper description of the item (e.g., Acme Wool Sweater).
- Missing Required Product Date (Missing Sell By Date): There is no product expiration, sell-by, or best-by date on the label or case, and Item Setup indicates that one should be present.
- Incorrect STOP Label (Incorrect Master Pack Labeling): This sub-defect only applies to e-commerce shipments. The STOP label doesn’t have “Mixed Merchandise | Receive as Breakpack” listed. Additionally, this sub-defect could include item information other than the postal code, or the shipping label may not have the Walmart Item Number as the Master Pack.
- Missing STOP Label (Missing Master Pack Labeling): This sub-defect only applies to e-commerce shipments. There is no STOP label on the Master Pack.
Hazardous Materials (Hazmat) Compliance
Hazmat compliance is crucial in helping Walmart’s associates handle your delicate or volatile items carefully and safely. Material marking requirements are separated by General Merchandise and Direct Import.
The sub-defects for hazmat compliance are:
- Hazmat Marking Missing: The case contains hazardous materials but lacks proper hazmat labeling.
- Hazmat Marking Covered: There are hazmat markings, but something (e.g., another label) is obstructing them. Hazmat markings must be clearly visible and legible.
- Lithium-Ion Marking Missing: The case contains lithium-ion batteries or other Li materials and lacks that marking.
- Lithium-Ion Marking Covered: There is a Li marking, but something is obstructing it.
- Limited Quantity Marking Missing: The case contains materials that are hazardous in large quantities, so it should contain markings indicating the limit.
- Limited Quantity Marking Covered: There is a marking indicating a quantity limit, but something is obstructing it.
Packaging, Pallet, and Load Quality
Phase 3 of SQEP addresses the need for packaging, pallet, and loading standards. These standards include edge crush test (ECT) compliance, pallet labeling, load separation by PO, and more. Non-compliance results in fines, depending on the type of defect. There are three defects, each of which has sub-defects:
- Packaging
- Palleting
- Loading
Packaging Compliance
With automation becoming the standard, it’s essential to prevent product damage in transit, so your packaging must meet Walmart’s standards. These are the sub-defects for packaging compliance:
- Missing Bottom Tray or Lid: The case requires a lid or tray due to the nature of its contents, and it does not have one.
- Loose Wrap: The shrink wrap around the package has loose ends or doesn’t fit tightly to the box.
- Poor Perforations: The carton’s perforation is so weak that the box opened during handling.
- Insufficient Fragile Item Packaging (Poor Packaging for Glass/Ceramic/Fragile): The contents are designated as fragile (i.e., easily break without careful handling), but the carton lacks proper packaging to secure the items within. Compliance with this sub-defect helps avoid broken items.
- Selling Units Not Secured: There is a lot of space within the carton, resulting in loose items. Alternatively, there may be extra space between the contents and around the edges of the box. Simply put, your carton is too large for its contents, and the items are loose and susceptible to damage.
- Loose or Metal Straps (Loose/Metal Straps or Bands): This sub-defect occurs in one of two ways: either the straps or bands do not securely adhere to the carton, or they are metal.
- Packaging Easily Crushed (Weak Packaging): The cardboard corrugate does not meet your packaging ECT standards.
- Insufficient Glue or Tape (Weak/Lack of Glue/Tape): The openings and flaps are not secured with enough glue or tape, or they have no adhesive.
- Overpacked/Bulging Case (Oversized/Undersized Case): The box is too small for its contents, and the sides are bulging out.
The calculation for packaging non-compliance is:
$200 per defect per PO + $1 per item
So, if you have 1 PO of 9 cases, and 3 of the cases have weak packaging, and 3 cases are oversized, and 3 cases have loose wrap, the calculation would be:
$609 = [$200 x (1 + 1 + 1)] + [$1 x (3 + 3 + 3)]
Palleting Compliance
Correctly palletizing your merchandise can help your products arrive at the DC unharmed and prevent shortage or damage deductions. Additionally, pallets must have correct labels and be the correct size.
There are four defects under Palleting, each with one or more sub-defects. These are:
- Pallet Labeling—Mixed Dates Labeling Missing/Incorrect: The pallet contains perishable items with different best-by or sell-by dates, and the “Mixed Date Pallet” label is either not on all four sides of the pallet or has incorrect dates or quantities.
- Pallet Securement—Poor Securement: Although the pallet arrived undamaged, it requires additional securing (e.g., shrink wrap or bands) for stability during handling at the facility.
- Pallet Securement—Bagged Items Missing Pallet Barriers (Bagged Item Missing Bottom Tray): The pallet contains bagged items (e.g., flats of bottled water), and there isn’t a tray, slip sheet, or tier sheet between the bottom layer of product and the pallet.
- Pallet Build—Pallet Overhang: The pallet contents are wider than the pallet’s dimensions, causing cartons to hang off the sides.
- Pallet Build—Exceeds Max Pallet Height (Exceeds Max Height for Trailer Type): The pallet is too high for the Walmart trailer. This most often happens with direct import suppliers or when the pallet is double-stacked.
- Pallet Build—Incorrect Ti: The pallet Ti (i.e., cartons per layer) doesn’t match the product’s pallet specifications in Item 360 or the item file. Ti/Hi is an important calculation because it lets the DC and store know how many items are on each level (Ti) and how many levels there are in total (Hi), and therefore, helps provide an accurate count.
- Pallet Quality—Poor Quality (Fair Quality): The pallet doesn’t meet one or more of Walmart’s published standards in its supply chain packaging guide. These can include broken or split boards, raised nails, metal repair plates, and more.
- Pallet Quality—Non-Compliant Pallet Size: The pallet isn’t within a quarter of an inch of the standard size for a full pallet. The pallet jack entry side should be 40 inches, and the forklift entry side should be 40 inches.
Some notes on palleting:
- You may use non-wood pallets, provided they are edge-rackable and meet Walmart’s standards (e.g., fireproofing, structural integrity, etc.).
- You may use standard-sized half and quarter pallets with approval.
- There are weight requirements for pallets, depending on the type:
- Grade A pallets have a maximum load weight of 2,100 pounds.
- Block pallets have a maximum load weight of 2,800 pounds.
- Walmart may approve of larger pallets for oversized items to prevent overhang. Contact your buyer or merchant for more information.
The calculation for pallet non-compliance is:
$200 per defect per PO + $4 per item or pallet
So, if you have a PO with 4 pallets, and 2 pallets overhang, and 2 pallets are of poor quality, the fine would be:
$416 = [$200 x (1 + 1)] + [$4 x (2 + 2)]
Load Quality Compliance
As part of the “right condition” aspect of SQEP, Walmart created standards for how well shipments travel. In addition, to help with the “right item” aspect, Walmart created standards for separating shipments and pallets on a trailer in transit to its facilities. The two defects for Load Quality are Load Stability and Load Segregation. These split into the following sub-defects:
- Load Stability—Shifted or Unstable: The freight on the trailer is leaning or has collapsed completely. In these circumstances, warehouse and DC workers must re-package or re-palletize the shipment to safely take it off the truck.
- Load Stability—Not Palletized: The freight is not on a pallet. This sub-defect is specific to staple stock.
- Load Segregation—Pallet Not Separated by DA and Staple: Distribution Assembly (DA) and Staple Stock (SS) POs are mixed within the pallet. DA items are products or goods not for resale (GNFR) that arrive unassembled at the distribution center and require assembly before going to the store. SS items arrive intact at the DC and are ready for immediate shipment.
- Load Segregation—Load Not Separated by DA and Staple: DA and SS cases from different POs are mixed throughout the trailer. In this case, the shipper must load SS items in the nose of the trailer, keeping POs together, and DA items in the back.
- Load Segregation—Same Item Not Grouped by Layer (Same Item/PO Not Grouped by Layer): Walmart requires each pallet level to have only one item type. This sub-defect occurs when multiple items of different types are on the same level (for example, cereal and napkins are on one layer).
- Load Segregation—Same Item & PO On Multiple Pallets (Same Item/PO on Multiple Pallets): A PO requested item quantities of the same type equal to or less than a single pallet, but the order is spread across multiple pallets. So, if your PO states that Walmart needs one pallet of 12 cases of soap, and you send two pallets with six cases each, you will see this sub-defect.
To sum up load quality compliance, ensure that your warehouse or 3PL does not mix POs, items, or DA/SS products on a single layer, pallet, or trailer. Also, ensure your pallets are stable and don’t need rework to unload.
The calculation for load quality non-compliance is:
$200 per defect per PO + $20 per item or load
So, if you have a trailer with 3 POs, each with 1 pallet, and 1 pallet falls over, 1 pallet contains DA and SS products mixed, and 1 DA pallet was in the nose, the fine would be:
$620 = [$200 x (1 + 1 + 1)] + ($20 x 1)
Tips on Staying Compliant
As you can see, defect fines can add up quickly. If you received defects for each non-compliant PO in this guide, it would add up to $2,466! The good news is that SQEP chargebacks are disputable in High Radius, and there are a few things you can do to avoid defects and stay compliant.
- First, read the Walmart Secondary Packaging Supply Chain Standards carefully for your merchandise alignment, item specifications, and shipping type. You can find this guide in Supplier Academy on Retail Link.
- Maintain and manage your documentation so that you can dispute invalid chargebacks.
- Optimize your supply chain with 3PL cheat sheets and standard operating procedures (SOPs).
- Check your SQEP scorecard at least weekly to stay on top of your defects and constantly improve your performance.
- Finally, regularly audit your third parties—including warehouses, trucking companies, EDI providers, and supply chain management—to ensure they are complying with Walmart’s SQEP standards.
Need help with SQEP defects? Let’s talk about disputing chargebacks, supply chain optimization, aligning your compliance, and using automation to manage your documentation.
More Posts
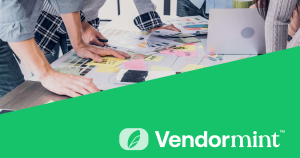
Avoiding Costly Mistakes: A Deep Dive into Compliance & Dispute Management with Major Retailers
Expert Strategies for Retail Dispute Management, Deduction Management, Retail Compliance, and Supply Chain Optimization
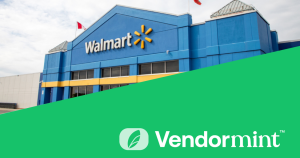
Walmart Profitability and Growth: Strategies for Suppliers in Uncertain Times
In today’s retail environment, consumer packaged goods (CPG) brands face mounting pressure from tariffs, compliance fines, operational inefficiencies, and increasingly complex relationships with major retailers like Walmart.
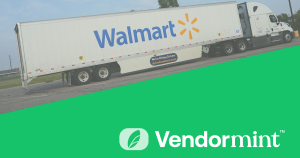
Walmart On Time In Full (OTIF) Compliance
Learn about the Walmart On Time In Full (OTIF) compliance program, including KPIs, metrics, and strategies for creating a compliant retail supply chain.
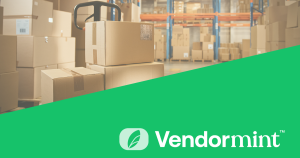
What Are OS&D Deductions?
What are OS&D deductions? Learn about overages, shortages, and damages, how they can impact your bottom line, and how to recover lost revenue.
When you realize
you're missing out
on all the insider info
Get in on the action and join the VendorWorld™ Newsletter—stay up-to-date with industry tips, tricks, and the latest trends.
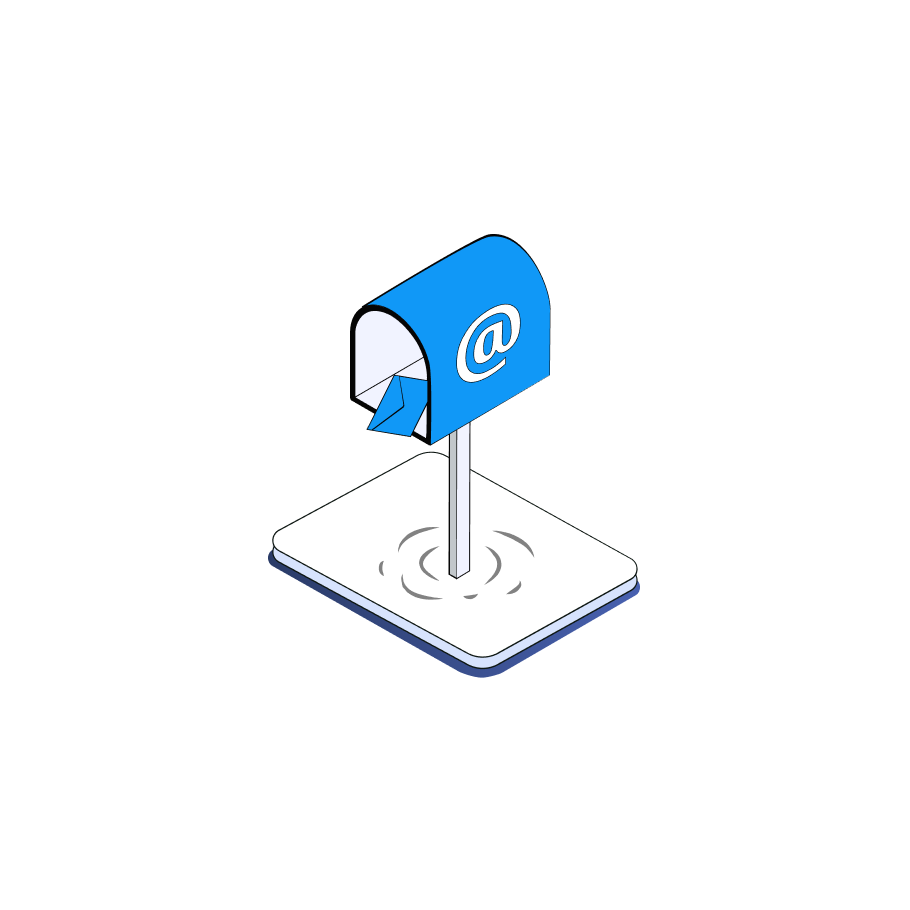